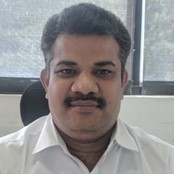
Biography:
Dr. Vijay Kulkarni (M.Pharm, Ph.D) has experience in pharmaceutical industry working on solid oral dosage forms development especially using hot melt extrusion or Twin screw processing for Solubility enhancement of poorly soluble drugs and for continuous Twin Screw Granulation. He has developed various formulations using this technology and transferred the technology to various pharmaceutical industries. He is also a recipient of Rising Star Award in Formulation Development, presented during FDD 2019 Conclave, Hyderabad. He has 15 years of research experience in pharmaceutical industry and academic research as formulation development scientist. He was a Post-Doctoral research fellow at University of Mississippi, USA working with Prof. Michael Repka
Abstract:
Statement of the Problem:
Pharmaceutical industry has faced increasing pressure to reduce costs due to the competition raised from generics production [1]. This has induced a shift from batch to continuous manufacturing because of several advantages (reduction in development and processing time, equipment size, manufacturing space, costs, quality control and less scale-up problems, increased control and ability to integrate process analytical tools) and due to this there are several initiatives are undertaken by regulatory agencies and pharmaceutical companies [2]. Continuous granulation using twin screw granulation (TSG) has emerged as an alternative to conventional batch granulation [3 & 4] and this is discussed in this presentation with case studies.
Methodology & Theoretical Orientation:
The continuous granulation sequence starts with 1) feeding the material (API+ excipient/s) through feeder (Gravimetric or Volumetric) in the twin screw processor as a premix blend or feeding the individual materials to continuous blender and then to the Twin screw processor, 2) addition of water or binder solution into the processor through pump, 3) mixing or kneading of the powder blend with water or binder solution by the specific configuration of screw elements, 4) drying and sizing inside the processor or through the integrated dryer and mill as shown in Fig 1. The granules and resultant tablets were evaluated for physical-chemical properties.